QMS-Management commitment for excellence
Management’s commitment to excellence shall be aimed at meeting our client’s demand and requirements for on time delivery all the time. It is the aim of BF-BCC to supply the correct resources in order to provide BF-BCC’s products and services on time and in accordance with stated clientele’s requirements. The products and services we offer in full or part are as follows:
- Electrical & Mechanical Construction
- Industrial Construction
- Power and Energy Construction
- Building Construction
- Base Maintenance Contracting Works
- Facilities Maintenance Contracting Works
The achievement of high quality and consistency calls for a systematic and disciplined approach by all employees in all activities associated with the Clientele’s order according to the principles of our Quality Management System. It shall be relevant to our organizational goals and the expectations and needs of our clientele.
Management assesses and evaluates the effectiveness of the quality management system by reviewing clientele complaints as documented in non-conformance reports, as well as audit results, execution of corrective and preventive action against BF-BCC’s quality policy and procedures.
The Quality Manual defines the management’s commitment for quality. The President and CEO has ultimate authority and responsibility for the effectiveness of the Quality Management System. The Quality Manager is authorized and is responsible for implementing and maintaining the Quality Management System defined in our QMS Manual and detailed in the Quality Procedures.
This statement represents my and our executive management commitment, on behalf of BF-BCC, to the Quality Policy.
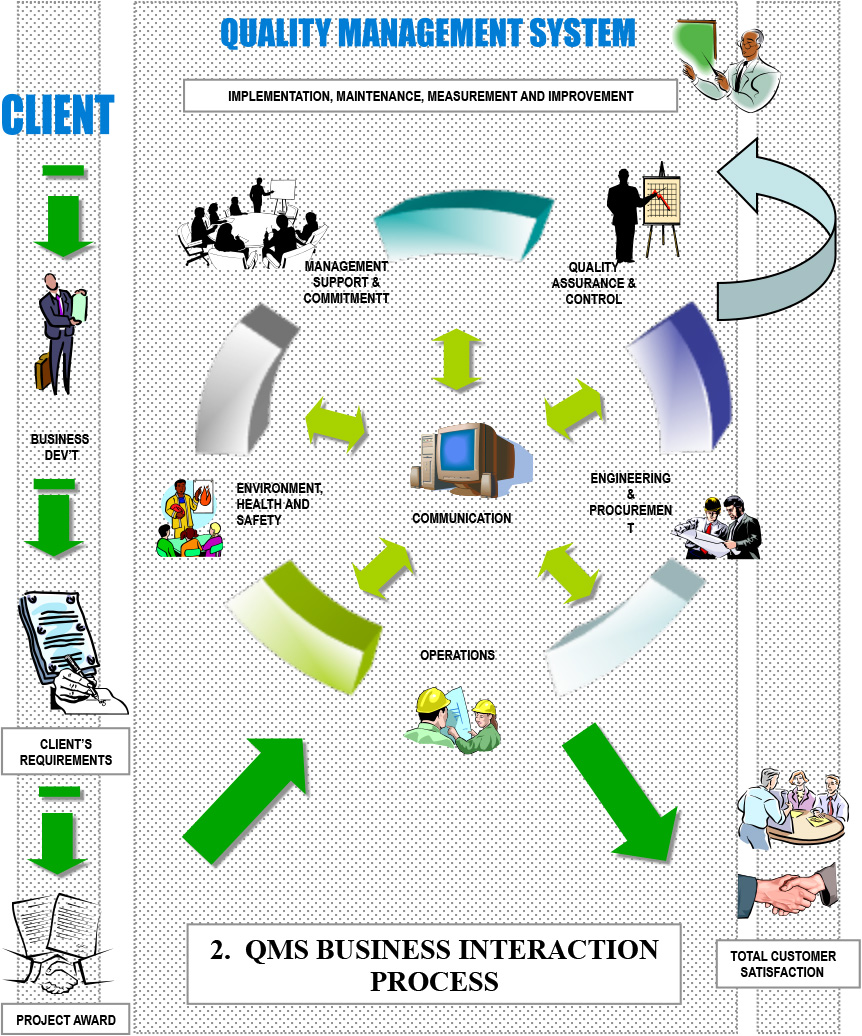
The Organization has establish, document and maintain this Quality Management System as a means of assuring our present and future customers that our product and services conform to specified requirements. BF-BCC’s QMS Manual will cover the Organization’s requirements and procedures in the application of the quality, environmental, safety and health management system. Work Instructions, criteria and methods, records and forms, among others, evidence our compliance to the integrated management procedures and shows the sequence and interaction of our QMS processes and business operations that include Executive Management, Finance and Administration, Legal, Business Development, Engineering, Operations, Accounting & Warehousing, Equipment and Transport, Audit, Quality Assurance and Control, and Environment, Health and Safety.
The Management ensures the availability of resources and information necessary to support the operation and monitoring of these processes. The Organization has established internal audits to monitor the interaction of our operational processes as well as analyze these processes for continual improvement. Scheduled management reviews are held to monitor measure and ensure conformity to the quality management system.
Control of Documents and Data
The Organization has established a Document and Data Control Procedure (BF-BCC-QMS-P01) to ensure that all pertinent QESH documents are controlled according to the requirements of QMS Standard. The procedure details how the documents and data are located, periodically reviewed, approved, revised and re-approved. The procedure also include guidelines to ensure that current versions of relevant documents (hard copy or electronic copy) are available at all locations where operations essential to the effective functioning of QMS are performed; that obsolete documents are promptly removed from all points of issue and points of use, or otherwise assured against unintended use; and that any obsolete documents retained for legal and/or knowledge preservation purposes are suitably identified.
Control of Records
The Organization has established a Control of Records and Records Management Procedure (BF-BCC-QMS-P02) to ensure that all pertinent QESH records required to provide conformity to the QMS standards are effectively operated and maintained. The procedure details how QESH records are identified, maintained legible, traced to activity or process, readily retrieved, stored, protected against damage, deterioration or loss, and how retention time is established and recorded.